Phase
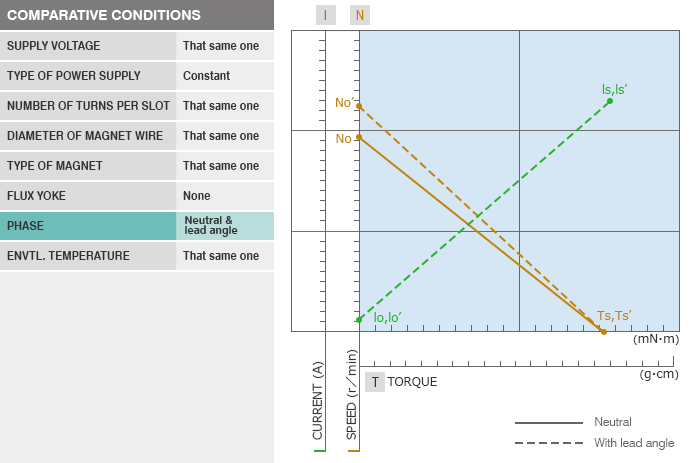
Phase refers to positional relations between the centerline of each polar magnet and the switching position of commutator segments and brushes.
Motors, assembled initially with neutral phase, runs under load lagging momentarily in the electrical phase due to its phenomenal armature reaction. Lagging in phase, therefore, is not preferable, since it causes efficiency, electrical noise, and life to become even worse. To avoid these situations, improved motors are assembled with forward brush-shifting that offsets the armature reaction during load operation to keep them on neutral electrically.
Let four performance characteristics for neutral (N0, I0, Is, Ts) and for leading in phase (N0', I0', Is', Ts'), respectively. Leading in phase causes the no-load speed N0' to slightly increase, as shown above, while all others stay almost unchanged and N0' rises 6 to 8% when leading 12 to 15°.
(Note: however, that stall torque can be obtained by using other than no-load and stall data, but in some cases Ts' may be smaller than Ts.)
A Point to Be Considered for Motors with Lead Angle
Motors with forward brush-shift, when run in the reverse direction, will have, due to resultant lagging phase angle, adverse effects resulting in poor commutation, undesirable electrical noise, and shorter life. For this reason, the motors must be run in one direction only.